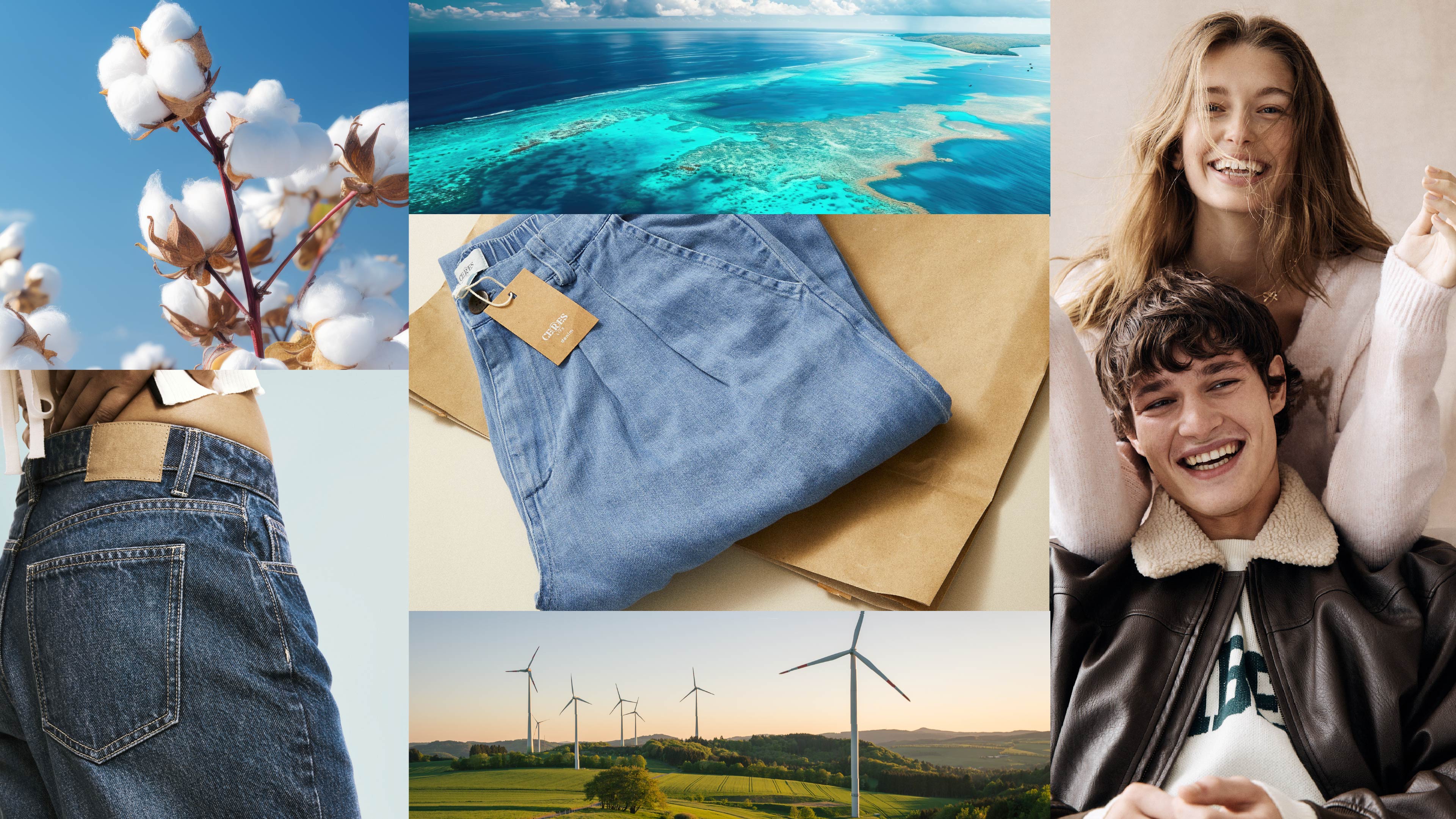
Sustainability
We’re a force for nature.
Making a positive difference? It’s what we’re all about. And when talking about sustainability, we’ve made some big changes that we’re proud of. But, we know there’s more to be done. And we’re taking action. ‘Cos our future depends on it.
We’ve got big goals, starting with going Carbon Neutral in our direct operations by 2030 and indirect operations by 2050. We’re also focused on Responsible Materials, Design and Production and our Plastics and Packaging journey.
So, from renewable energy to Better Denim and much more, we’re all about reducing our impact.
To learn more about Our Commitments, click here.
Change starts with us
Fashion is made to be loved and lived in every day. As a business built on fashion and Good, we know we’re responsible for caring for our planet and its people in everything we do.
We’re listening, learning and responding; always. Because we know big change starts when we bring our people and customers along on the journey. It’s a constantly evolving movement. 24/7. 365 days a year. And not just because it’s good for business, but because we couldn’t feel good about our business if we didn’t.
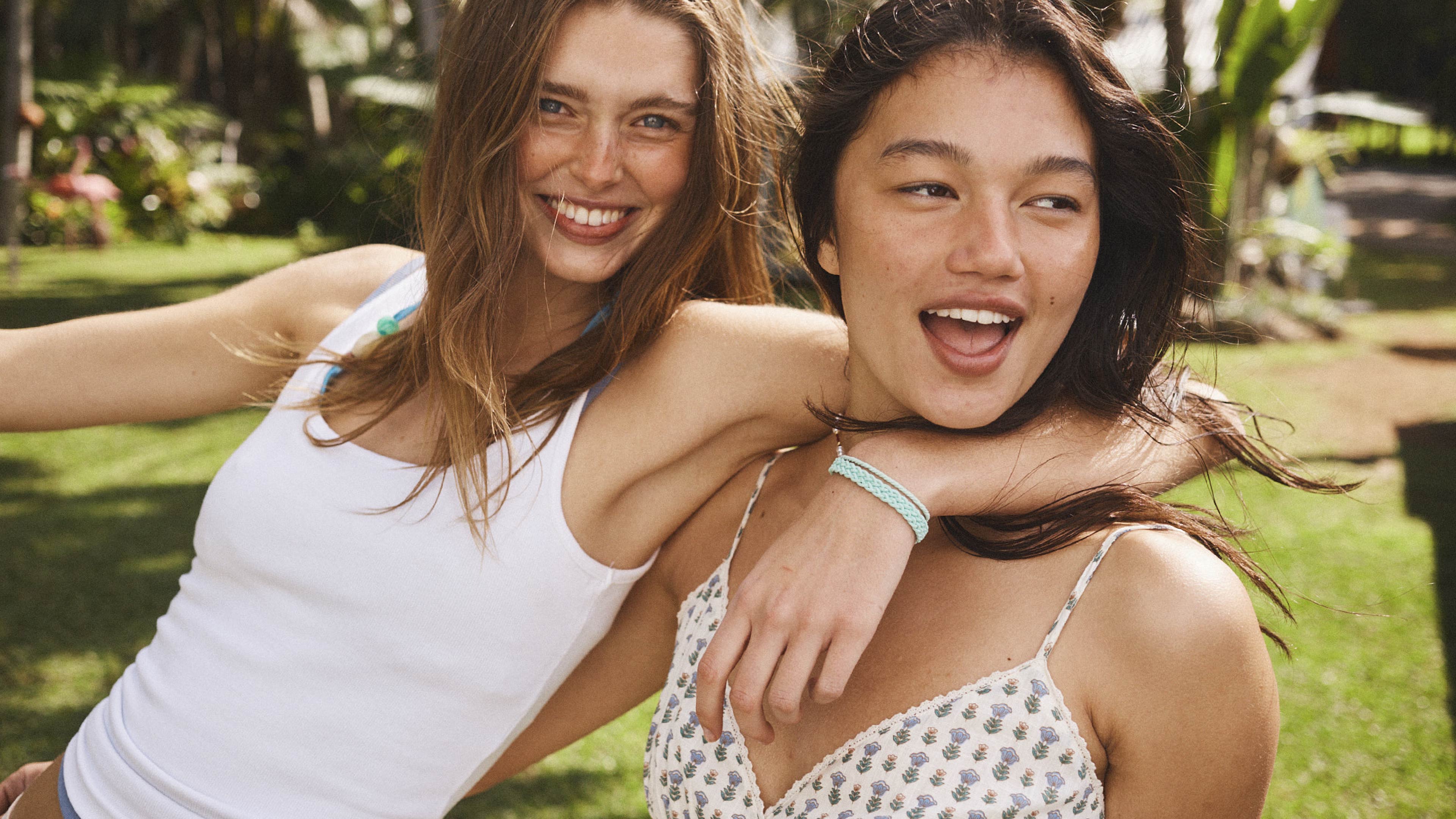